Jak se vyrábí procesory I. - Co je waffer a proč Intel zdržuje?
25. 6. 2014 08:00 Rubrika: Technologie Autor: Jakub Pavlis
Před pár dny se na našem webu mihla krátká zpráva o tom, že Intel nespěchá s vývojem výroby velkých, 18'' wafferů a že jeho konkurenti, zejména TSMC a Samsung, by ho mohli v této oblasti technologicky přeběhnout. Co to ale vlastně waffery jsou a k čemu jsou dobré? Přečtěte si první díl naší dvoudílné minisérie.
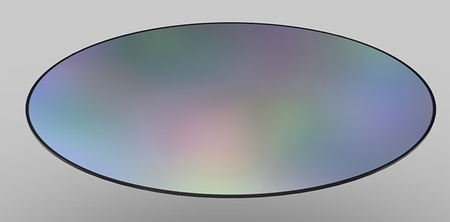
Nejdříve jakás takás definice: Waffery jsou tenoučké pláty vyleštěného monokrystalického křemíku, které sloučí jako základ pro výrobu čipů – ať už jde o v nadpise zmiňované procesory (Samsung patří mezi největší výrobce ARM procesorů) nebo třeba paměti RAM i NAND (opět Samsung nebo právě TSMC), ale i čipů pro bezdrátové signály, Wi-Fi, Bluetooth (TSCM vyrábí zařízení pro Qualcomm, AMD, Broadcom...).
Vyrábí se na půdorysu kruhu, což je dáno technologií výroby, jak uvidíme dále, ovšem samotné produkty – čipy – jsou obvykle čtvercové či obdélníkové. Po okrajích kruhu tak vzniká odpad – přebytečný materiál se musí odřezat. Tudíž waffer o větším průměry nabízí procentuálně menší odpad. A to již je na ceně výrobků dost znát. Když se kolem roku 2000 přecházelo z 200mm wafferů na 300mm, skokově klesly ceny o 30 – 40 %. Je pravda, že vinou vyšší náročnosti práce s většími waffery i nutnými investicemi do strojového vybavení továren se tentokrát očekává úspora maximálně do úrovně 20%. Proč o to ale Intel nestojí?
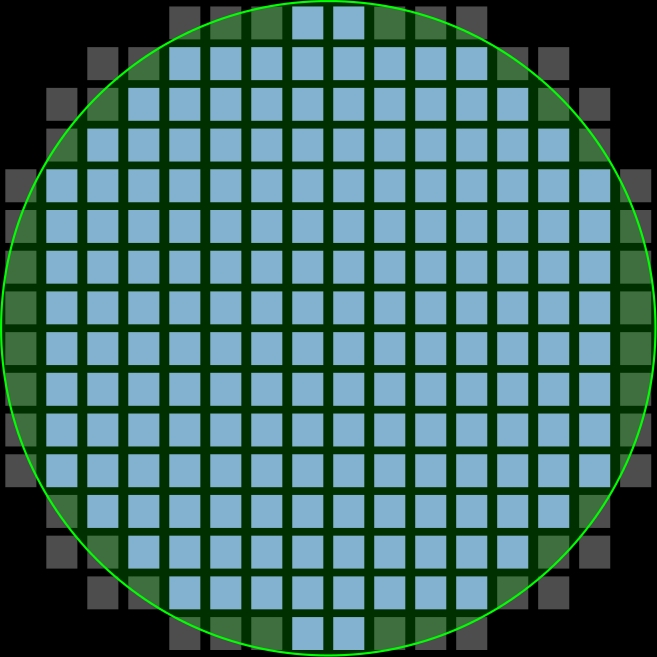
Zjednodušený nákres odpadu při výrobě čipů z wafferu
Intel především vyrábí jen velice úzký segment produktů, velkou většinu jeho obratu tvoří procesory na platformě x86 (s integrovanými grafickými kartami), trh s čipsety je s procesory velmi pevně svázán a SSD pořád tvoří jen okrajovou produkci. A na poli x86 procesorů nemá Intel prakticky konkurenci, AMD ovládá jen zlomek trhu a funguje do určité míry jen proto, že Intel potřebuje „konkurenci“ kvůli tomu, aby se vyhnul působení amerických federálních zákonů o monopolech, jinak by měl jistě sílu AMD z trhu vyšachovat (konkurenčně nebo nepřátelským převzetím, to nehraje roli). Nic ho tedy nenutí k tomu šetřit na výrobní technologií wafferů, stačí mu aktualizovat návrhy a sem tam posunout výrobní litografickou technologii (tick-tock systém).
Naopak pro firmy, které působí na trhu, kde je konkurence obrovská (zejména paměti RAM a NAND, procesory pro mobilní aplikace...), je zlevnění výrobu v jakémkoli jejím bodě velkou konkurenční výhodou. Dnes převažují waffery s průměrem 300 mm (11,8'', v anglicky psaných zdrojích je o nich obvykle referováno jako o 12'') nebo dokonce 200 mm (8''), které ovšem vytváří více „odpadního“ křemíku. A hyperčistý křemík opravdu není levná záležitost. Přechod na 450mm waffery (18'') navíc v podstatě zdvojnásobí použitelnou plochu, na jeden waffer se tak vejde více čipů, odpadnou tedy logistické meziakce – přeprava 925 µm tenkého plátu také není úplně bezriziková – a výroba se zrychlí. A čas jsou, jak známo, peníze.
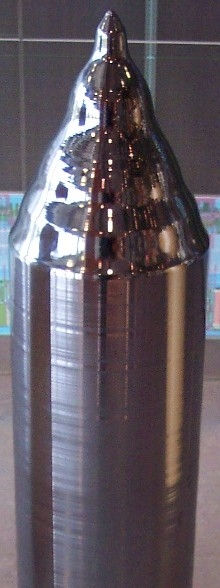
Artifikální monokrystal čistého křemíku
Přechod na větší waffery ale má i praktické nevýhody. Především jsou ingoty mnohem těžší a objemnější, což klade větší nároky na práci s nimi, očekávají se prolémy s hustotou kvůli gravitaci (větší ingoty se budou více „natahovat“ vlastní vahou) nebo problémy s udržením rovného řezu tak, aby nedocházelo k přílišným ztrátám při leštění do roviny. Navíc, výrazně větší ingoty budou také podstatně delší dobu tuhnout a vychládat, to jsou jen další problémy.
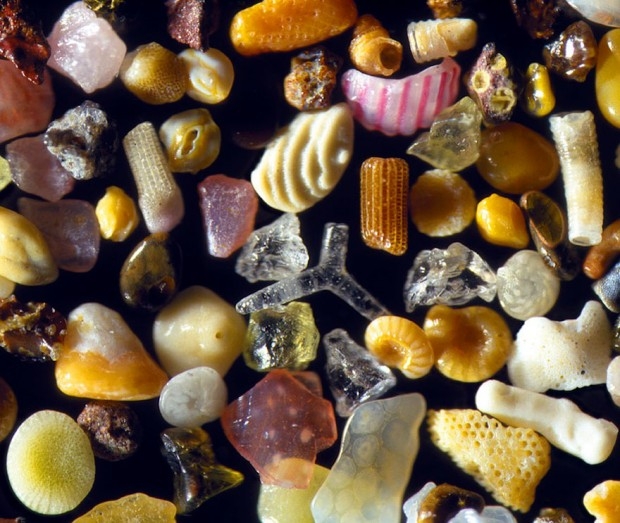
Písek pod mikroskopem
A jak se tedy procesory vyrábějí? Na začátku stojí obyčejný sklářský písek, s vysokým obsahem oxid křemičitého. V obloukové peci se taví na grafitové elektrodě, takže se uvolňuje CO2 a zbývá poměrně čistý křemík. V elektronice je však potřeba čistota s přesností na čtyři až pět desetinných míst, je tedy třeba projít fází čištění. V té se používá zonální tavení – na dlouhé křemíkové tyči se rozpaluje postupně vždy jen část, těžší usazeniny se udržují právě v polotekuté části a postupně klesají ke konci vertikálně umístěné tyče. Její konec se po celém procesu odřízne. Druhou možností je vytváření těkavých křemíkových sloučenin (trichlorsilanu nebo chloridu křemičitého) a jejich odpařování na křemíkovou desku za teploty kolem 1100 stupňů Celsia. Oběma způsoby však získáme polykrystalický křemík, k výrobě je ovšem třeba monokrystalického, to znamená, že všechen materiál je usazen do jediné krystalické mřížky.
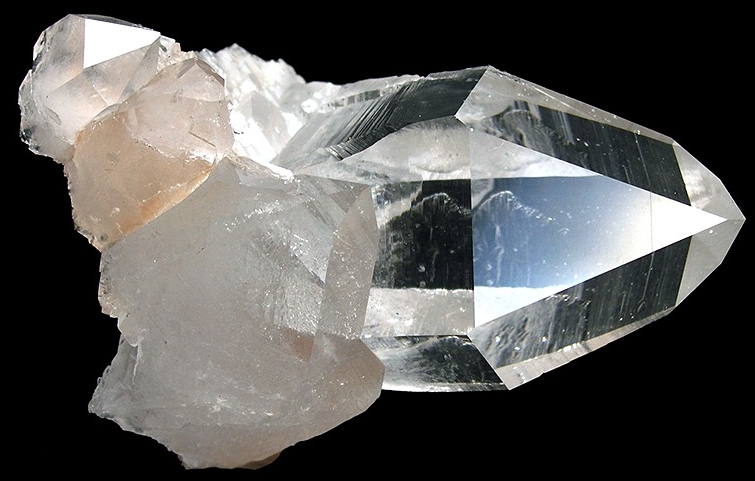
Přírodní krystal oxidu křemičitého - křišťál
Monokrystalické struktury se obvykle dosahuje tzv. tažením z taveniny, kdy se roztavený křemík za současné rotace „táhne“ na zárodečním pulsujícím krystalu. Výsledkem je křemíkový ingot, který má poměrně přesně kruhový průřez a požadovaný průměr (dnes obvykle 12'', do budoucna 18''). Takový ingot váží kolem 100 kg a může být několik metrů vysoký. Dále se soustruží a leští po plášti do přesně kruhového tvaru. Po vyleštění se řeže vodním paprskem. Laser se nepoužívá, protože by znovu natavil křemík a narušil jeho monokrystaličnost, u vodního paprsku toto nebezpečí nehrozí, navíc se vodní paprsek sám „chladí a maže“ :-) . U 12'' wafferu mají pláty tloušťku 775 µm, se zvyšujícím se průměrem se samozřejmě zvyšuje i síla desky, aby zůstala zachována alespoň základní strukturální pevnost. V době prvních Pentií Intel používal 4'' a 5'' waffery s tloušťkou 525µm, potažmo 625 µm.
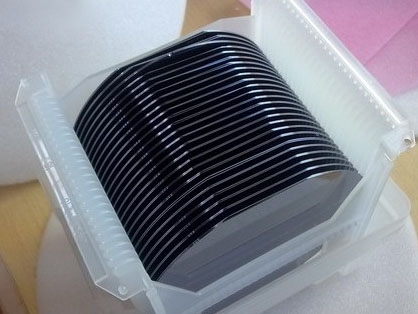
Hotové waffery připravené k dalšímu použití
Po fázi řezání nastupuje leštění, které opracovává povrch wafferu k absolutní dokonalosti, musí být perfektně rovný a hladký, aby se na něj dal bez obtíží „tisknout“ čip. K této problematice ale v příštím díle seriálu.