Jak se vyrábí procesory II. - Fotolitografie a výhledy
2. 7. 2014 08:00 Rubrika: Technologie Autor: Jakub Pavlis
Minulý týden jsme se seznámili s výrobou waferů v článku a dnes se můžeme podívat, co výrobci čipů dělají s nimi a jak dlouhou cestu musí taková deska čistého křemíku ještě urazit, než se dostane v kovovém pouzdře a osazená do motherboardu až k Vám na stůl.
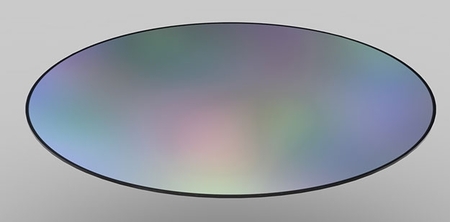
První díl najdete zde "Jak se vyrábí procesory I. - Co je waffer a proč Intel zdržuje?".
Na jedné straně slévači a chemici čistí křemík, aby bylo možné vyrobit procesor. Jeho cesta ovšem začíná svým způsobem i na jiném místě, než je pískovna. Totiž v počítačích návrhářů a designérů, kteří procesor vymýšlí. Nejprve se navrhne struktura a její softwarový model. Ten běží obvykle mnohem pomaleji, než skutečný procesor, a slouží k testování logiky a plnění úkolů (například verifikace používání instrukčních sad apod.). To je samozřejmě náročná a také do značné míry automatizované práce, kterou zajišťují velké mainframové superpočítače. Model se neustále vylepšuje až do chvíle, kdy je chybovost přijatelná (prakticky každý návrh procesoru jde do výroby s nějakými „mikrochybami“, které řeší logika počítače a ne konkrétní užívání procesoru pak mají dokonale zanedbatelný vliv). Vzniká tak velké množství prototypů, u kterých se ladí rozmístění částí procesoru kvůli zahřívání jeho různých částí, věci kolem spotřeby, problémů je vždycky více než dost. Výsledkem je návrh takzvané masky, tedy jakéhosi stínítka, přes které se nasvěcují wafery. A zde můžeme zase navázat v továrně u vyleštěného kusu křemíku.
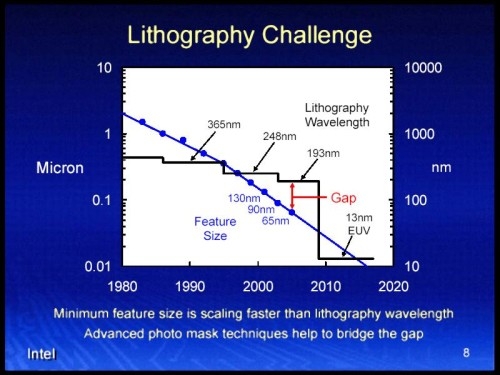
Máme-li hotový wafer, je zapotřebí do něj „vyhloubit“ jednotlivé transistory tam, kde je to zapotřebí. Vzhledem k minimálním rozměrům tranzistorů (Intel pracuje s 22 nm technologií, jeho konkurenti s 28nm, přechod na ještě drobnější rozměry nás čeká zanedlouho) je možné je tisknout vlastně už jenom světlem. Na wafer se nanese světlocitlivá vrstva. Její nanášení je dalším důvodem, proč wafery musí být dokonale kruhové – rychle se roztočí a barva je dokonale pokryje díky odstředivé síle. Pak přichází na řadu fotolitografie. Světlocitlivá vrstva se ozařuje přes masku UV paprsky. Masky jsou samozřejmě mnohem větší (obvykle zhruba 4x) než výsledný procesor, pro soustředění světla se používají ještě čočky. Proces se opakuje podle návrhu procesoru i více než dvacetkrát.
Světlocitlivá vrstva se samozřejmě dopadem UV záření naruší, takže je právě jen narušená místa možné smýt speciálními roztoky. Následuje fáze leptání, kdy se odhalené křemíkové části leptají, zatímco ty, které zůstaly pod nenarušenou světlocitlivou vrstvou, zůstávají neporušená. Tím dojde k vytvoření prohlubní a kanálů, tedy tvarů konečných tranzistorů. Po vyleptání všeho potřebného následuje znovu pokrytí světlocitlivou vrstvou a fototisk, tentokrát ovšem slouží světlocitlivá vrstva k ochraně křemíku proti vysokorychlostnímu bombardování ionty, které jsou urychlovány elektromagnetickým polem a slouží právě k vyplnění předtím vytvořených prohlubní a změně způsobu vedení elektrického proudu v jinak homogenním křemíkovém monokrystalu.
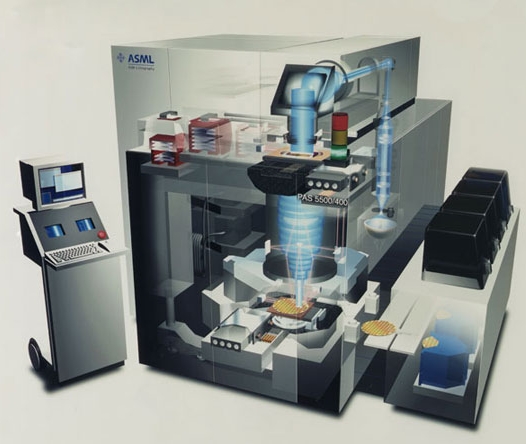
Po iontovém dopingu se tranzistory překryjí tenounkou izolační vrstvou a elektrolyticky se pokovují – vznikají tak měděné spoje mezi jednotlivými tranzistory a částmi procesoru. Celý proces se opět několikrát opakuje, takže roste počet vrstev nad sebou, dnes se běžně pracuje i se dvěma desítkami vrstev. Stoupá tím tedy počet masek, které je třeba používat, a také výrobní náklady. Podle výrobců představují právě náklady spojené s fotolitografií více než polovinu nákladů na celý procesor (a to připočtěte materiál, propagaci, logistiku, údržbu továren a platy zaměstnanců...).
Po kompletním vytvoření procesorů na waferu následuje první kontrola a testy funkčnosti. Až do této chvíle se používá wafer jako celek a teprve po testování se vodním paprskem řeže na jednotlivé procesorové destičky. Počítá se i s určitým procentem odpadu, obecně se říká, že ve střední části waferu vznikají kvalitnější čipy a směrem k okraji kvalita klesá. Podle výsledků testů se pak také třídí čipy a nastavují se jejich tovární hodnoty. Čím je čip kvalitnější, tím větší snese zatížení. Po rozsortování jsou tedy destičky z jednoho waferu základem pro různé modely procesorů jedné architektury (teoreticky tak vedle sebe mohly být vyrobeny tak cenově rozdílné procesory, jako jsou dvoujádrové Core i3 a Core i5). Nefunkční a poškozené destičky se pak vracejí na začátek koloběhu a recyklují se pro výrobu nových waferů.
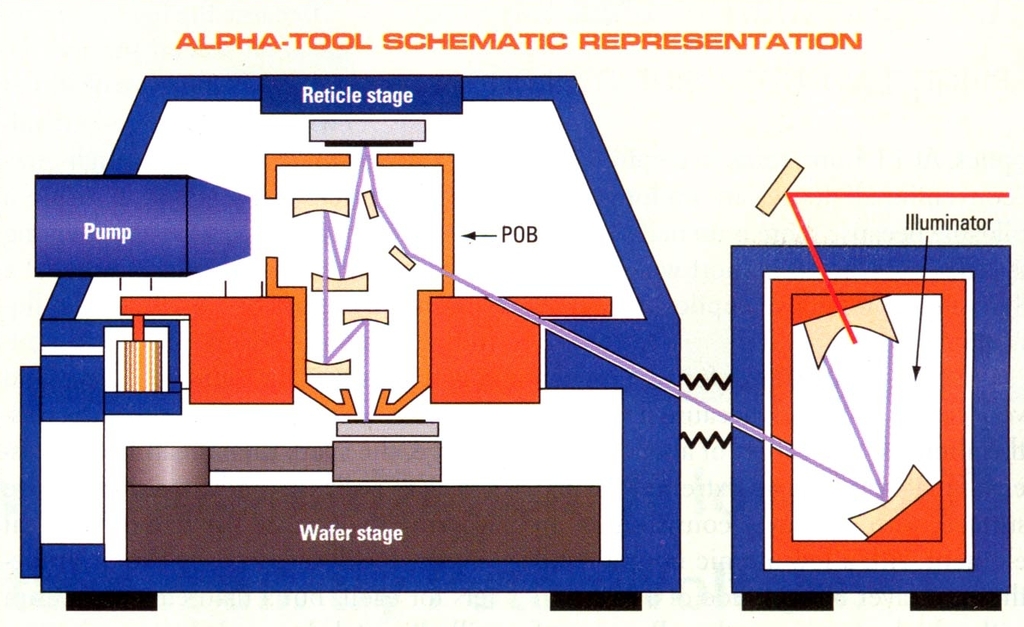
Po roztřídění se destičky spojí s podkladovou deskou s piny a překryje kovovým chráničem, který jednak brání fyzickému poškození velice křehké křemíkové součástky, jedna rozvádí produkované teplo a zajišťuje kontakt s chladičem. Následuje finální testování, roztřídění a samozřejmě balení do plat pro OEM výrobce nebo v malém procentu případu do boxů přímo pro koncové zákazníky. (což se mobilních čipů netýká prakticky vůbec).
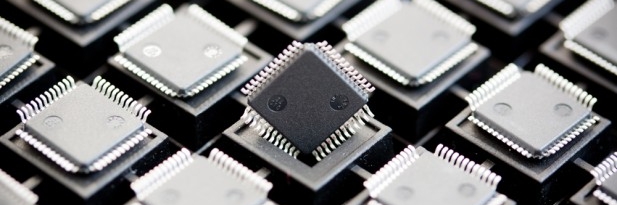
Budoucnost vývoje čipů je dnes trochu nejistá. Intel směřuje do oblastí mezi 10 a 5 nm, kde již bude problémem udržet elektrický proud v jeho vymezených drahách, dochází ke skokovému zvyšování odporu a začínají platit spíše zákony fyziky kvantové než té „klasické“. Řešením je podle Intelu další rozvíjení 3D struktury transistorů (započaté tri-gate technologií) nebo nové materiály. Jednak se mluví o rovnoměrnějším uspořádání atomů v krystalické mřížce, jednak o nanomateriálech jako je grafen (speciální forma uhlíku). Jejich výroba je ovšem velmi drahá, technologie nevyzkoušené a grafen má i vlastnosti, které nejsou pro výrobu celých tranzistorů zcela vhodné – například je u něj jen těžko dosáhnout dokonale nulového stavu (bez elektrického náboje). A vrstvené struktury mají zase potíže s účinným chlazením. Výrobci však věří, že se jim ještě nějakou dobu povede naplňovat Moorův zákon – každých 18 měsíců dvojnásobek tranzistorů za stejnou cenu.